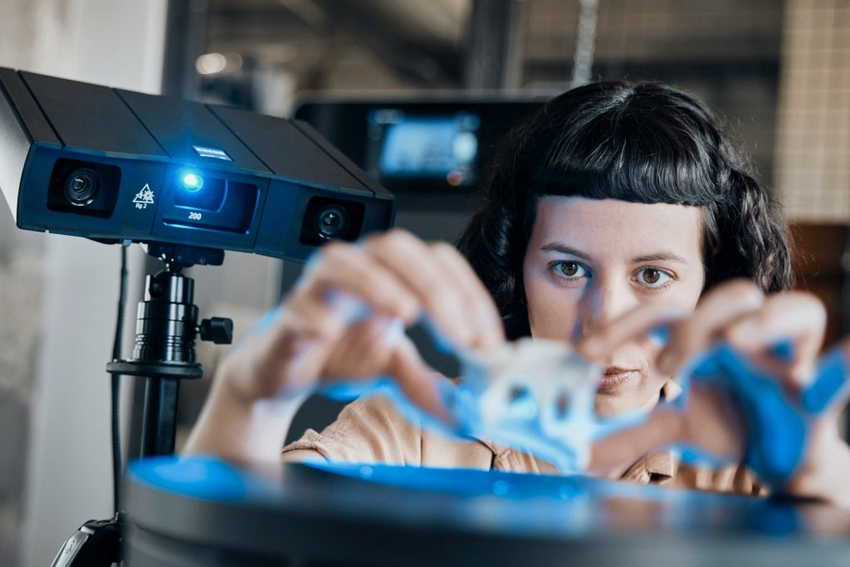
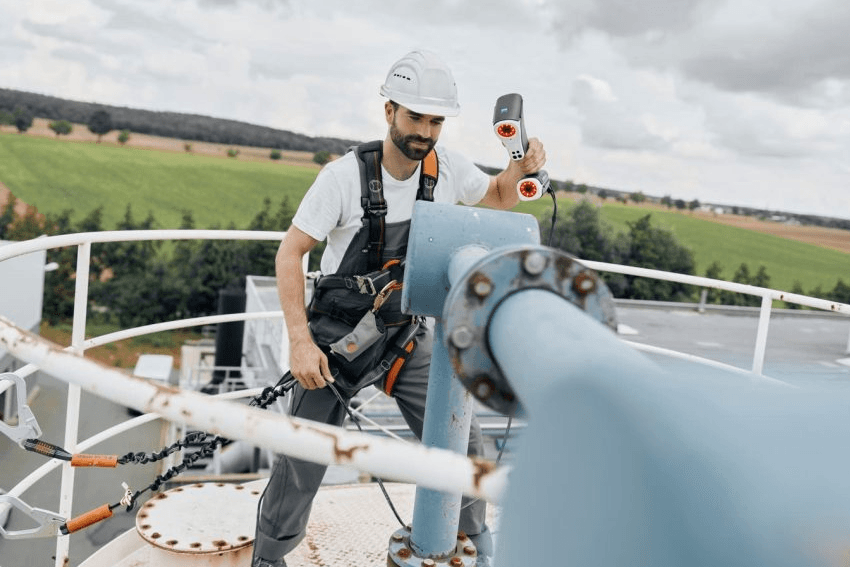
Optical measurement systems do not obtain their accuracy through expensive and maintenance-intensive precision mechanics, but rather rely on opto-electronics, precise image processing and the latest mathematical algorithms. A few precision scales and automated calibration that can be performed by the customer give the measurement system its precision. As a result, there is no loss of accuracy due to wear, even under adverse conditions. Measurement uncertainty is certified in the same way as tactile measurement systems using ball bars or gauge blocks. More than 17,000 GOM measurement systems worldwide guarantee the dimensional quality of automotive, sheet metal, casting and injection molded products, as well as turbine blades and wheels. In most cases, detailed analyzes are not enough for a simple i. Good/Not Good O. evaluation, but form the basis for optimizing production and machine parameters as part of a value-added measurement process.
Solutions for the industry
Aerospace
GOM's optical 3D measurement systems greatly contribute to meeting the complex requirements of the aerospace industry. 3D optical measurement technology enables precise quality control of all products in the industry.
GOM systems support the aerospace industry and its suppliers by providing accurate part geometries and deformation analysis. This data is used in R&D, manufacturing, and MRO to understand failure modes and ensure proper quality and overall aircraft safety. By building a complete digital twin of the aircraft and its systems, GOM optical metrology sensors, coupled with powerful analysis software, help the aviation industry build and maintain aircraft faster and safer.
If the average global citizen travels on average once a year, planes must meet quality standards, inside and out. Aircraft structures, systems and interiors are incredibly complex with thousands of parts, high customization and extreme quality requirements to ensure safety. GOM optical metrology technology streamlines aircraft development, quality assurance and maintenance checks.
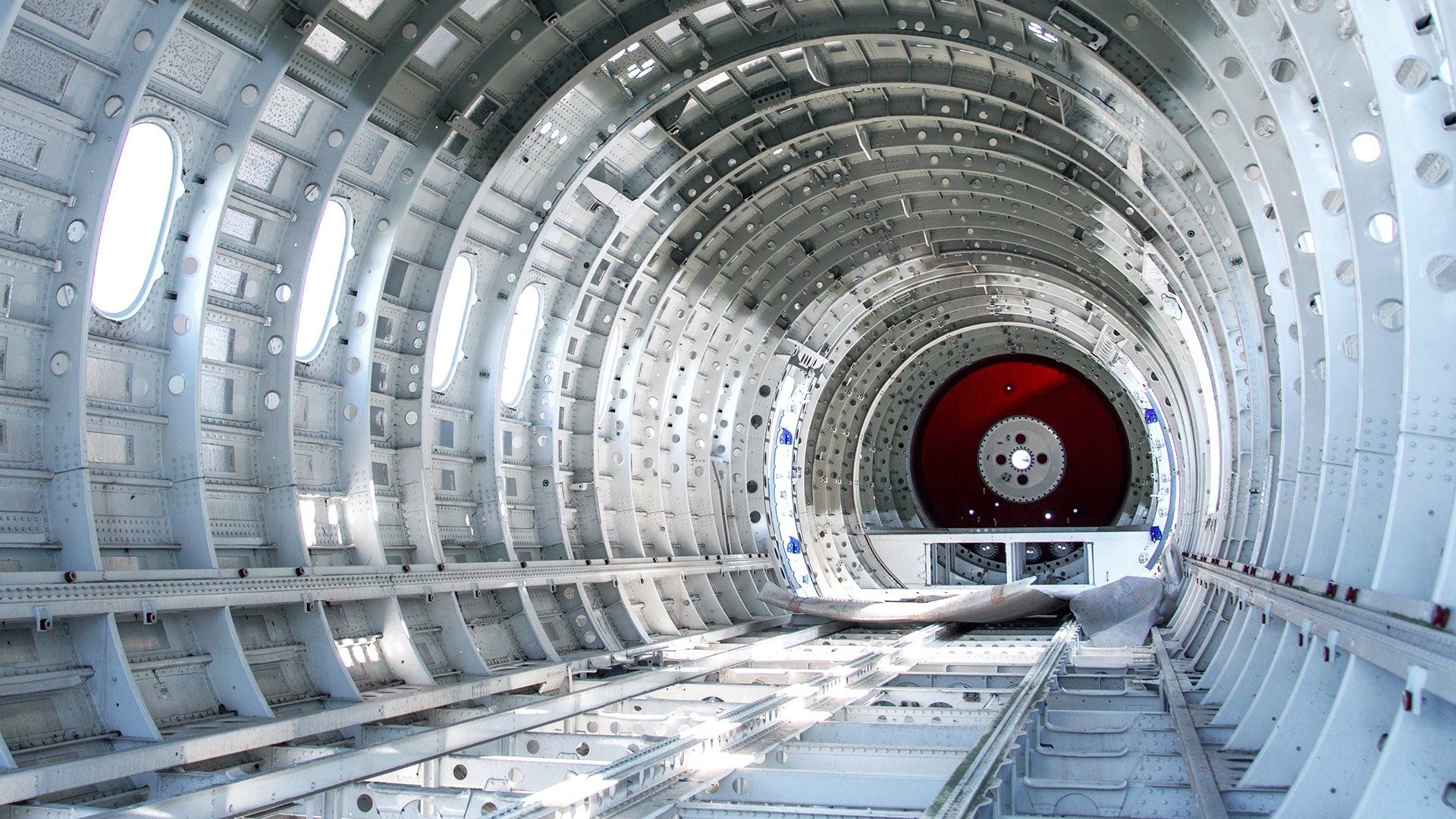
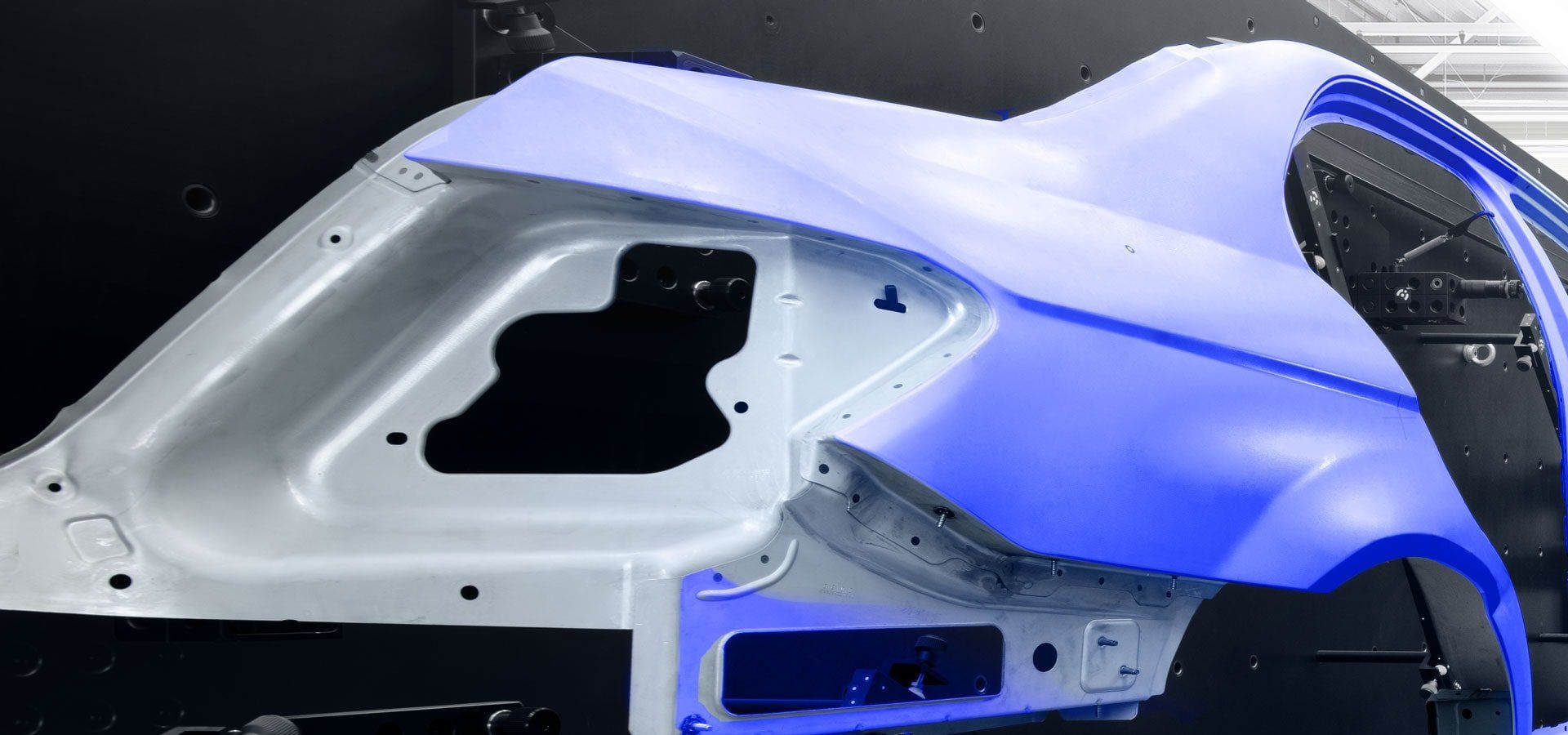
automotive
The increasingly automated automotive industry benefits from full-field geometry acquisition from 3D scanning. By implementing GOM products in product development, simulation, design, and QA, the entire new product development is optimized.
In the automotive industry, GOM systems are used throughout the development process of a new car. In product development, measurement data provides information about the characteristics of materials and the behavior of parts. The results influence simulation and engineering. In increasingly automated production quality control, full-field geometry acquisition via 3D scanning provides the database for inspecting shapes and tools, castings, plastic and sheet metal parts, as well as complete assemblies and bodies. .
Consumer goods
In the production of consumer goods, optical measuring systems from GOM are an optimal complement in all production steps. 3D optical measurement technology ensures efficient product development and production and helps significantly shorten ramp-up times in product launches.
Short product cycles, cost pressures, and high-quality requirements force consumer goods manufacturers to develop and produce products efficiently. Therefore, GOM systems are used for all production processes, from material design and testing to tool and mold manufacturing, inspection and first article production to assembly analysis and load testing. During tool buying and first article inspection, full field measurement results provide comprehensive data on the geometric and dimensional accuracy of manufactured parts. In this way, start-up periods for product launches can be significantly reduced.
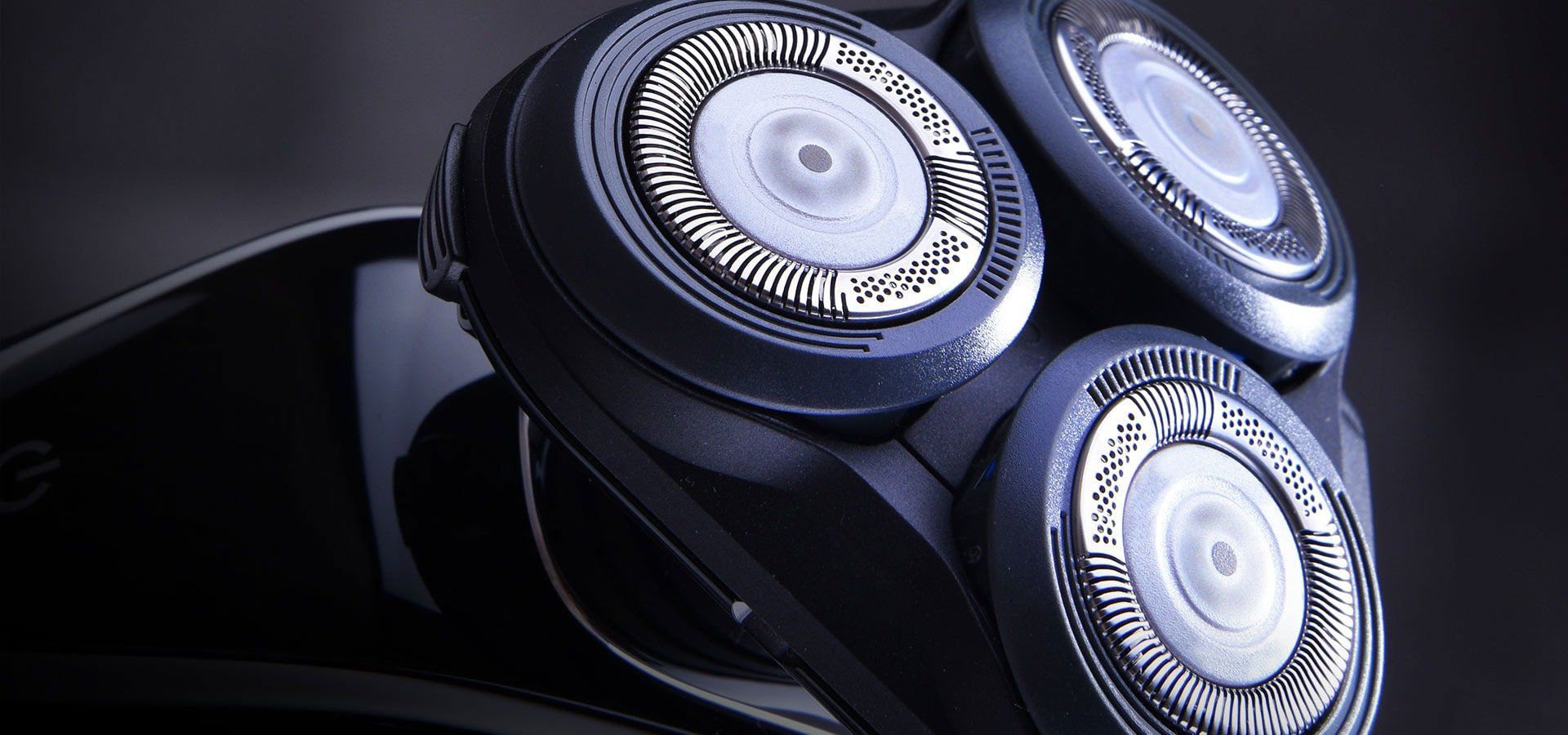
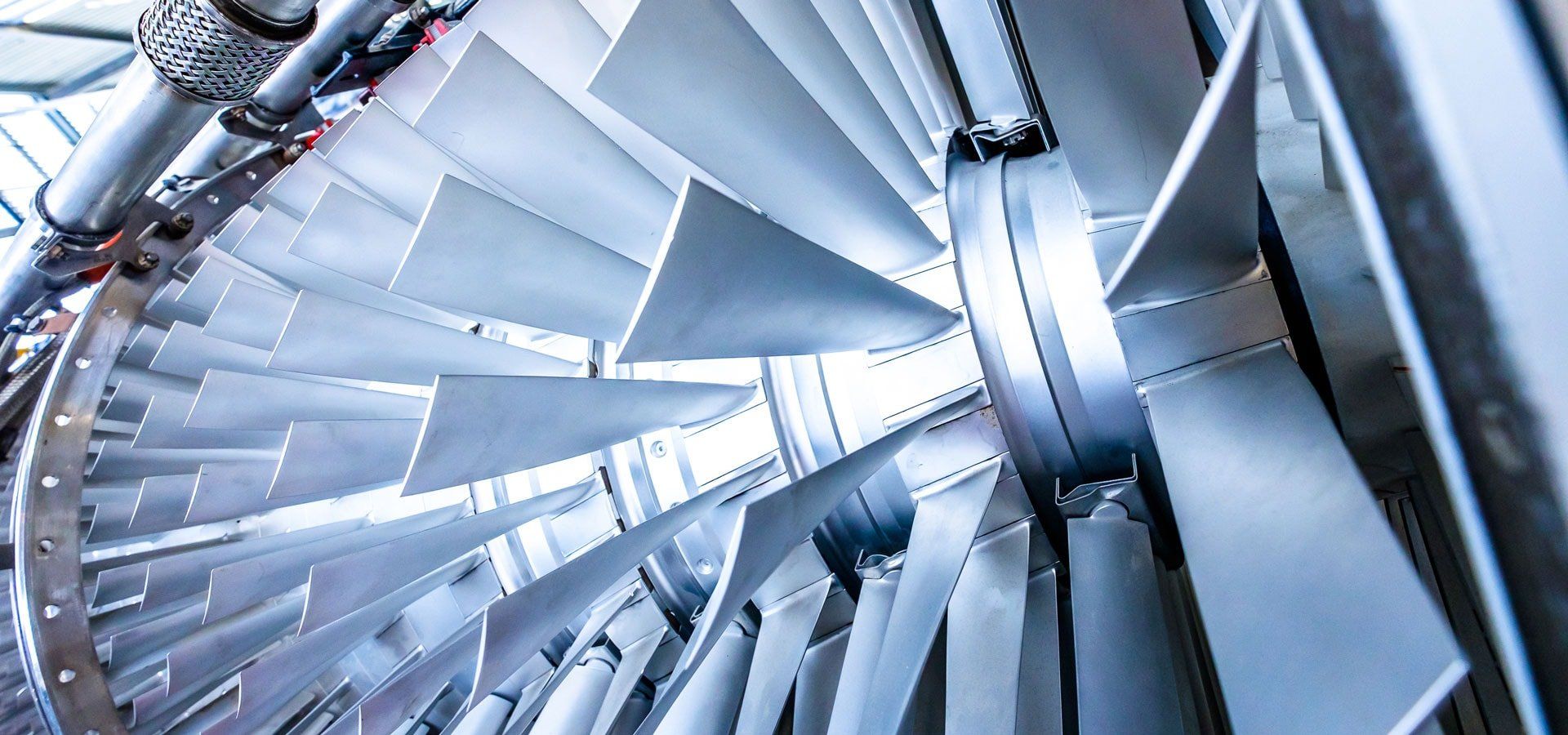
Energy generation
GOM systems are suitable for the inspection of complex free-form surfaces, such as airfoils on gas and steam turbines and turbochargers. The systems support the introduction, inspection and final acceptance of different production technologies, as well as maintenance, service and upgrades.
Optical 3D scanners are suitable for quality control of complex free-form surfaces. Therefore, they are used for the inspection of airfoils of jet engines, land-based gas and steam turbines, and turbochargers. Many turbine blades are manufactured by casting, forging, milling, and grinding processes. In quality control, GOM systems support product launch and final inspection and acceptance in various production technologies. Color deviation maps as well as 2D and 3D analyzes of shape, position and thickness help draw conclusions about manufacturing effects. 3D metrology also speeds turbine maintenance, service and upgrades by identifying defective areas or parts that need to be replaced, verifying that sufficient material has been applied, and inspecting the post-processing procedure.
Transport
In transportation, GOM solutions are especially relevant for quality control. GOM products are used in railway engineering, shipbuilding and utility vehicles to ensure the quality of means of transportation.
The modern transportation industry requires precise and efficient production control, fast and cost-effective maintenance and repair. To meet this demand, GOM offers mobile optical measurement technology systems to check complex geometries and dimensions of parts and even the entire ship's body and hull for quality control. The acquired 3D measurement data is also used through reverse engineering for the rapid manufacture of replacement parts. 3D data is used to speed up processes and improve the efficiency of engineering and repair, whether for trains, ships or utility vehicles.
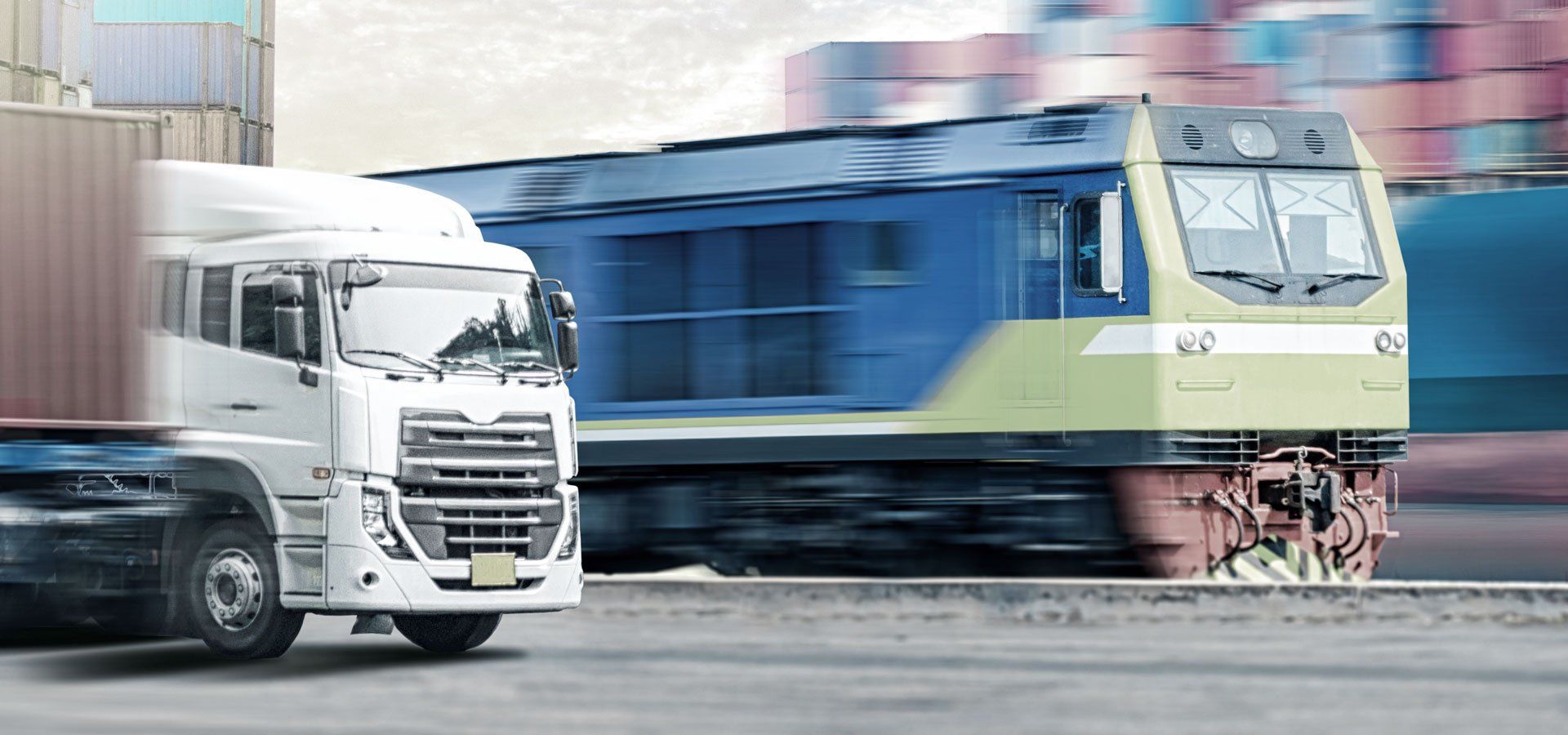
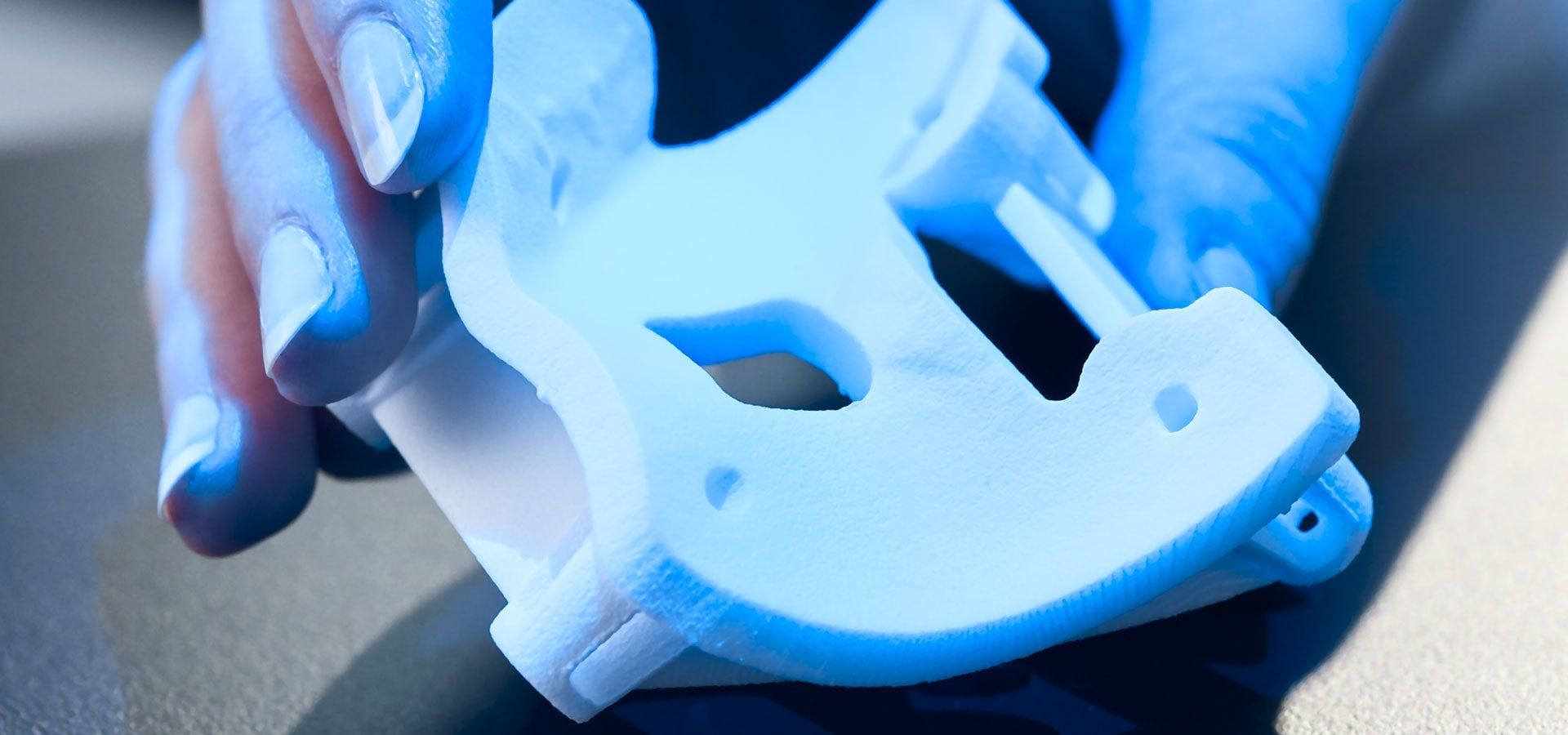
Medicine
GOM systems are suitable for various applications in medical technology and biomechanics. 3D measurement technology is an inherent part in the implementation of dynamic analysis in biomaterials, such as stress, load and fatigue tests.
Medical technology places particularly high demands on the quality of materials and products, as this has a direct effect on our health and well-being. To fulfill this responsibility, development and innovation are first preceded by years of research work. 3D optical metrology supports these processes significantly, whether in biomechanical material testing, for dynamic analysis of implants and prosthetics, or in quality control and product development of medical devices.
Solutions for manufacturing processes
metal forming
GOM products are widely used throughout the metalforming process chain. They support consistent quality control, from determining material characteristics to production control and assembly analysis.
GOM optical 3D measurement systems are used in stamping, bending, drawing, pressing and forming process chains to ensure constant quality control: they are used to determine material properties. They help optimize the design and simulation of parts and tools. They speed up tool testing and first article inspection. Optical 3D measuring systems also ensure efficient production control and serial assembly analysis.
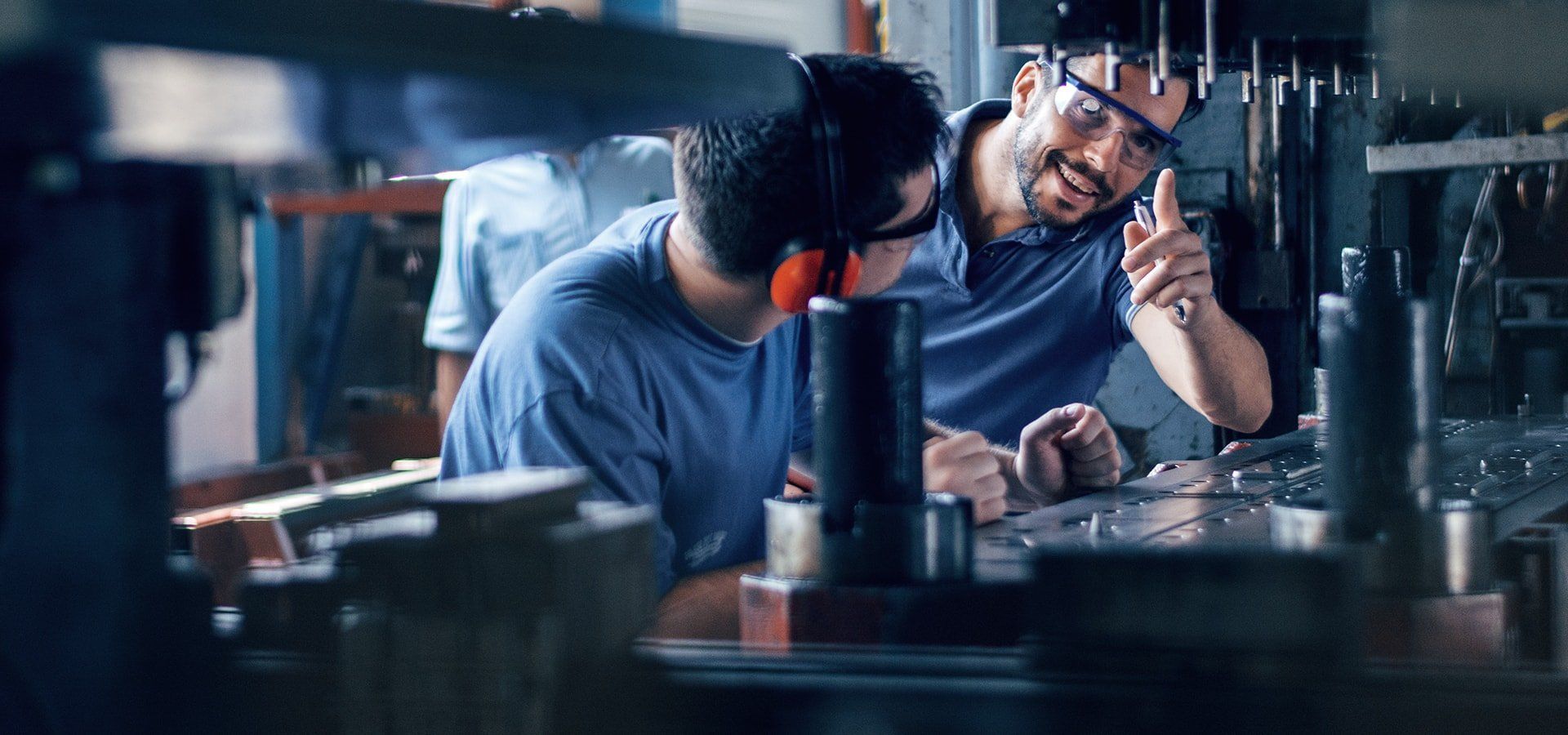
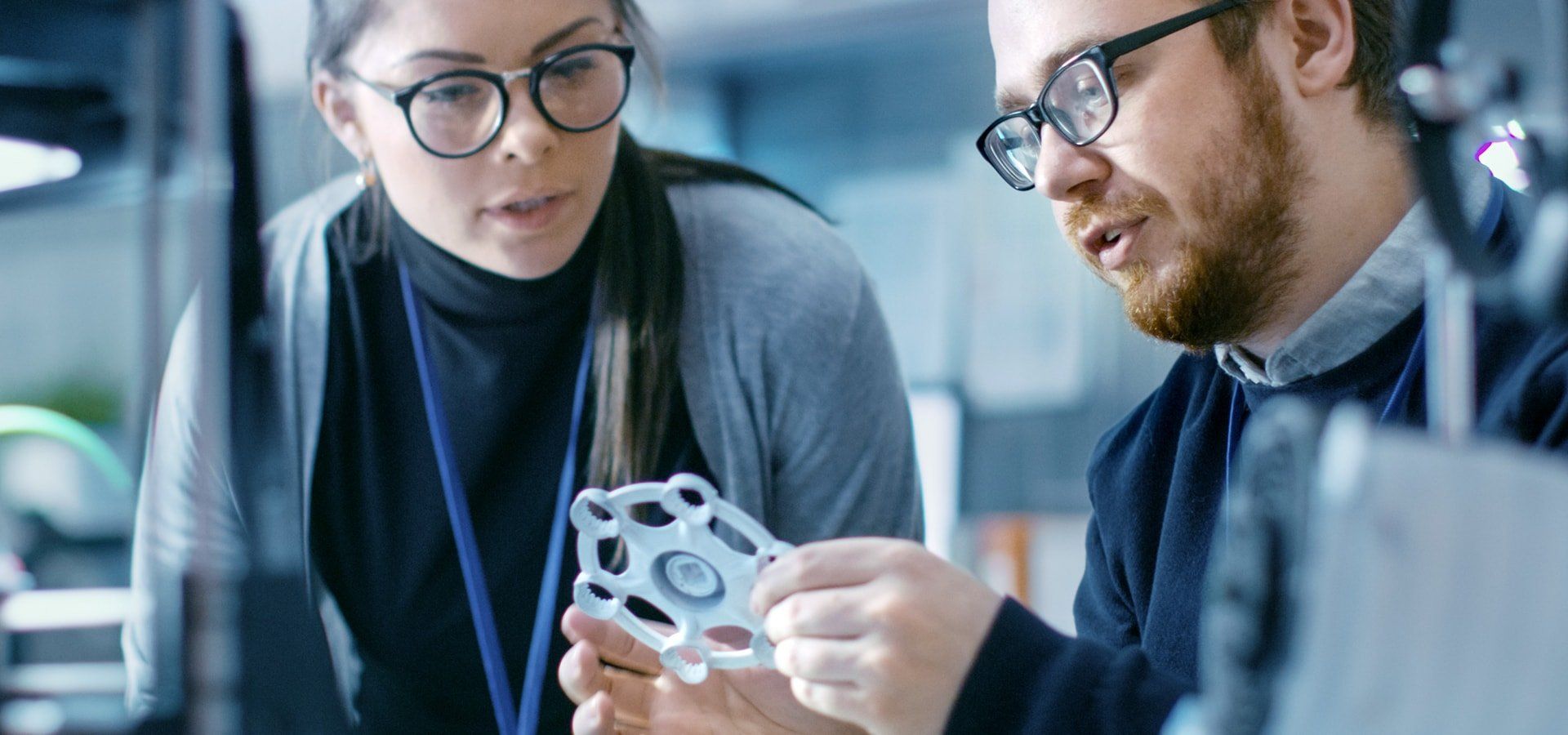
additive manufacturing
Highly individual parts with complex geometries are often a challenge in quality control. With GOM's flexible systems, individual process steps are optimally supported, from 3D scans to formation analysis and final evaluation by the powerful GOM software.
The industrialization of additive manufacturing continues. Whereas additive manufacturing was previously used primarily for small-scale prototyping, today many industries are increasingly using additive technologies to optimize their processes and configure their products. The efficient production of injection molds using 3D printing and the use of additive manufacturing in die casting often involve components with complex geometries. GOM's non-rigid 3D measurement systems ensure process reliability in quality control, from material validation to 3D scanning and final evaluation using comprehensive GOM inspection software.
plastics processing
Precise optical 3D measurement technology supports and accelerates nearly every phase in the injection molding, blow molding, and thermoforming processes, from prototyping and tooling to initial sample test reports to sample analysis. assembly and load tests.
In plastics engineering, 3D measurement technology supports and accelerates all phases of the injection molding, blow molding and thermoforming processes: from prototype and tooling construction to first article inspection reports to analysis of assembly and load tests.
ATOS is an optical 3D coordinate measurement system that enables non-contact measurements of full surfaces of prototypes, electrodes, tools and injection molded parts, regardless of the size of the object. Unlike tactile measurement techniques, this method even captures complex freeform contours quickly and completely. Full field surface measurements ensure faster first article inspection and tool-specific correction, reducing production lead times. For quality control accompanying production, both measurements and the entire evaluation process can be automated.
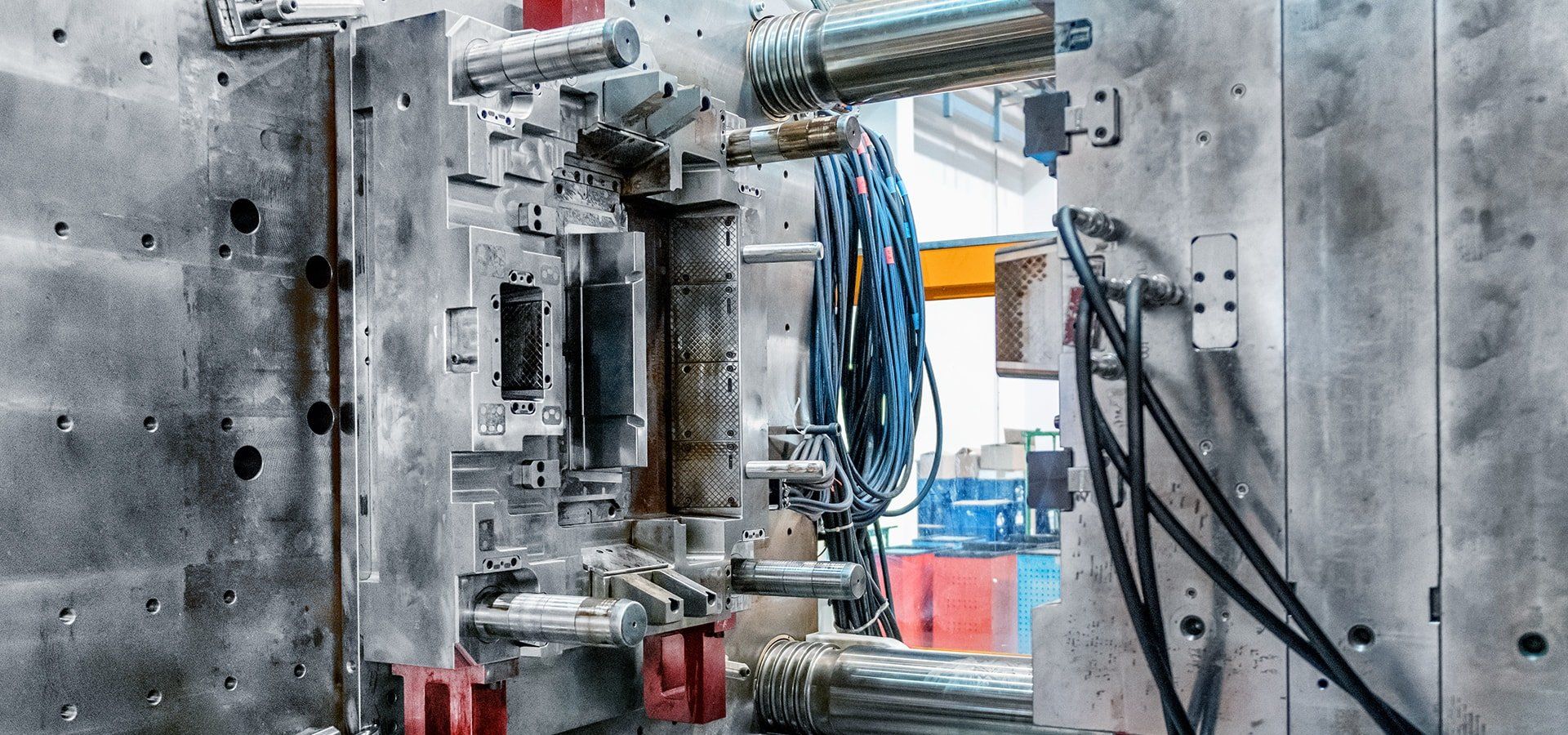
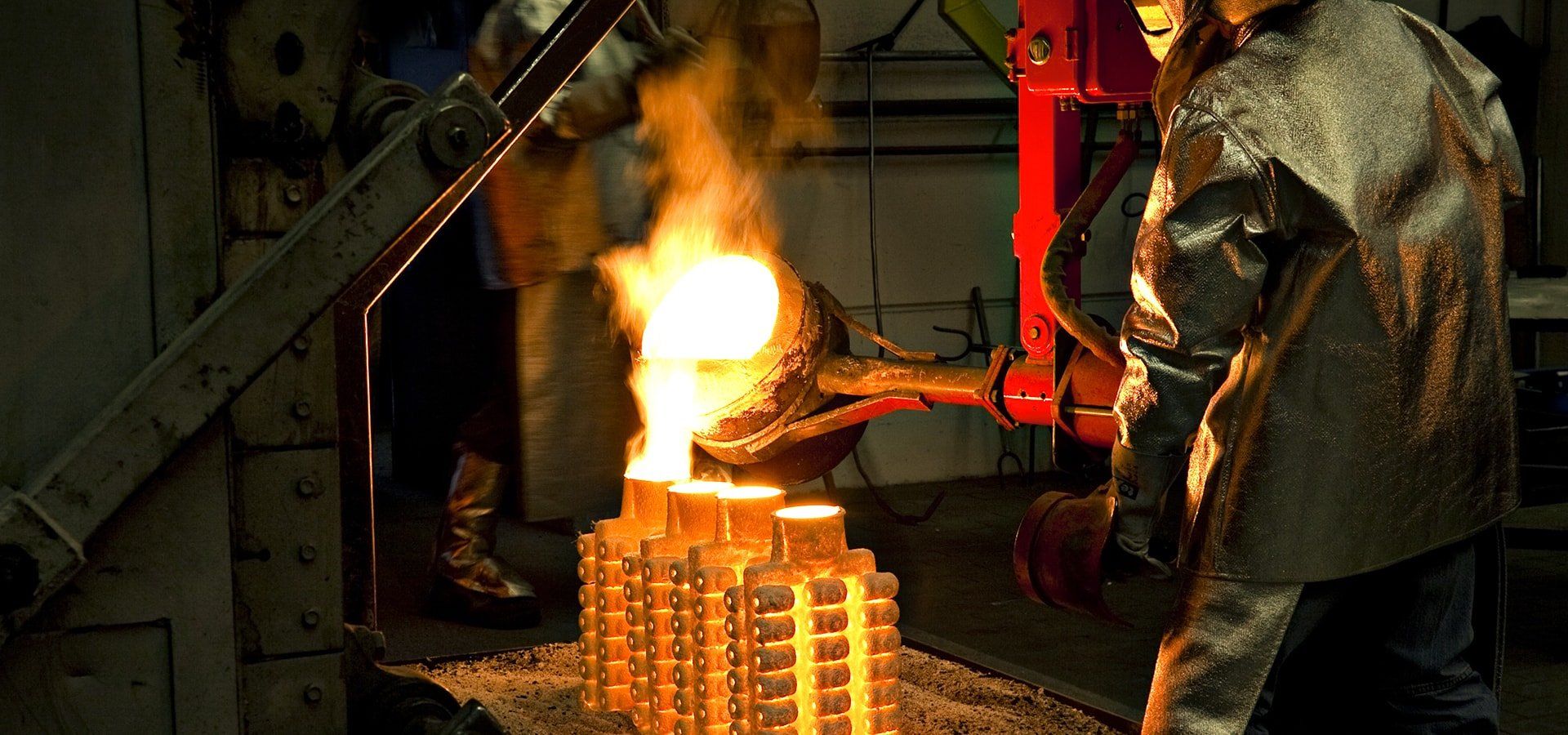
Metallurgy and foundry
In the metallurgical and foundry sector, GOM products are used for permanent quality control. Process steps such as simulation validation, tool testing, first article inspection, and production control are carefully controlled with GOM products.
GOM measurement systems are used in sand, die casting and investment casting processes to ensure constant quality control: from simulation validation through accelerated tool testing and first article inspection to production control and CNC machining.
GOM systems enable inspection planning based on design data. In pattern and mold making, specific tool and pattern correction and fit inspection of mold halves, cores and sliders are possible. During the test, the shape and dimensions of the castings are checked: part geometry, material thickness, shrinkage and warpage. All measurement and inspection processes are automated for production quality control.